GAC Honda: Pioneering Excellence in Intelligent Manufacturing
-
#Intelligent Operation
-
Equipment Utilization Rate99.1%
-
Equipment Failure Rate2%
Reduction
-
Annual Spare Parts Cost$15,000
Reduction
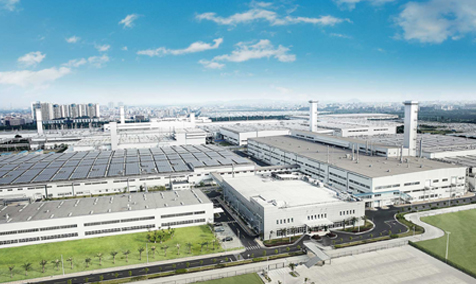
Challenge
After years of development, GAC Honda is determined to enhance workshop equipment control for better response to sudden processing anomalies. There's an urgent need to improve proactive monitoring by introducing predictive maintenance, ensuring optimal production to meet demand. Additionally, to minimize management waste and enhance efficiency and quality, there is a focus on further optimizing tool management to boost competitiveness in the QCD industry.
Solutions
GAC Honda collaborates with iROOTECH for smart factory development, achieving seamless connectivity in their engine plant through an industrial IoT platform. This collaboration enhances equipment efficiency and precision, leading to significant improvements in quality, cost, and delivery. The implementation of iROOTECH's IoT platform notably elevates GAC Honda's performance across key operational areas.
- AI Prediction and Maintenance Optimization
AI intelligent predictive analysis for WE2 SR welding stations, AF2 predictive maintenance. Utilizing modeling analysis to provide timely and effective references for high-precision, efficient equipment operation.
- Intelligent Factory Construction and Full Connectivity
Full connectivity is achieved in the engine factory through the iROOTECH Industrial IoT Platform. Utilizing 5G, machine vision, big data, cloud computing, etc., to establish full connectivity and data-driven operations for equipment, production lines, and the entire factory.
Benefits
- Optimized Operations
The integration of the iROOTECH Industrial loT Platform at GAC Honda Plant connects all elements of the automotive manufacturing process, providing meticulous calculations to offer the most optimal solutions for business operations. The integrated crop rate of equipment in the assembly shop reached 99.1%.
- Data-Driven Precision
The intelligent transformation covers four major workshops with over 300 devices on the platform. Utilizing 5G, machine vision, big data, and cloud computing, it digitizes production equipment data, offering timely and effective references through modeling analysis for high-precision and efficient equipment operation.
- Preventive Maintenance and Cost Savings
Through IoT-enabled frequent vibration and load detection, equipment status visualization and real-time intelligent calculations prevent defective products, reducing batch scrap by over 50%. Tool and equipment spare parts save 15,000 USD per year, with tool management optimizing replacements based on wear status, resulting in a 5% increase in lifespan.
Share
"By integrating the iROOTECH Platform, we have achieved comprehensive improvements in the QCD (Quality, Cost, Delivery) domain. As the platform functionalities were implemented, we experienced significant enhancements in our business processes. All available data is quantified, and various digitization projects based on the iROOTECH platform have brought considerable convenience to our daily work. This aligns perfectly with our initial goal of venturing into IoT. The overall application effects are also very pronounced."
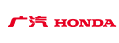
Tan Yongjian, IT Department, GAC Honda (Zengcheng)
How Can We Help
-
Talk to Our Expert
Connect with our global experts for customized solutions and support.
-
Request a Custom Solution
Create tailor-made solutions that align perfectly with your business.
-
Access to the Resource Library
Explore our resources to fuel your digital transformation and master the nuances of Industry 4.0.